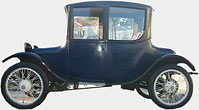
- Miles Twete’s 1921 Milburn Light Electric: top speed 28mph, range 90 miles, worm drivetrain, and a Coal-burning foot warmer.
- Chris Jones’ EV Conversion Plan. He’s put together some helpful information, including a battery comparison chart and a drive train comparison.
- It was inevitable that hybrid kits, of some sort or another would start showing up. And like some of the new “hybrids” that will be coming from auto manufacturers, not all of them are meant to improve fuel efficiency. Check out the Electrocharger kit, to increase the initial rate of acceleration. Essentially a beefy alternator with a heavy duty belt connecting it to the engine shaft. They claim that it should improve fuel efficiency, but won’t have data to support this until later this year.
- No idea on the propulsion means for any of these, but some very interesting cars in this Art Car Fest flickr set.
- A123’s new nanotechnology-based lithium-ion batteries will start showing up in power tools soon. A123 claims its battery offers twice the power density of comparable ‘old-technology’ lithium ion cells. I’ve volunteered to be an EV tester…no word back yet. ”:^)


Now, if Eve was a Dewalt* instead of a Ford, you probably could get them at Wal-Mart, jer-ree
* A123Systems has begun full-scale mass production of the smaller format battery packs.
I take issue with some of the results that Chris posted on his site regarding EV drivetrains.
Where the different drivetrain configurations are compared, the DC options are shown as “rpm and Tq limited”, as compared with the AC versions. While it is completely true that the AC motor systems develop peak RPM and Tq that is higher than that of a DC system, the DC systems are more than adequate.
Also, the “direct drive” (no trans, clutch etc) DC system is shown needing two motors. After extensive “testing” and simulations using the tools on Uve Rick’s site, I have found that a single 8” or 9” DC motor is MORE than enough to direct-drive a conversion. The RPM limits of a typical DC motor are 6,000 RPM on the high side. With careful gear (RWD) selections, most conversion vehicles can be run at 5,000 motor RPM at 60 MPH or so.
Remember, higher motor RPM requires higher voltages, and LOWER amperages so there are lower I^2 losses. This results in longer range and component life.
Furthermore, a DC motor makes peak Tq at “stall”, exactly where you need it to get a vehicle moving from a dead stop.
With a “fixed” (transmissionless, or trans fixed in 2nd for example) DC drive, the city efficiency is slightly lower than optimum, but the weight and expense savings are substantial. Not to mention the additional space that is avaialbe when the motor occupies the space that the transmission USED TO.