Not an EV · 21 March 06
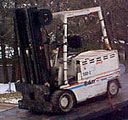
First off Darin asked that I add the disclaimer that he is NOT making an electric vehicle (yet).
Just because him and his buddy bought a used forklift (EV parts) and had it shipped, at some expense, to their house doesn’t mean they are making an EV (yet).
Sure, Darin has been asking questions on the EVList about turning the parts from a forklift into an EV, but that doesn’t mean he’s making an EV (yet).
Now that the disclaimers are out of the way let’s see what Darin is up to…

From Darin:
The theoretical donor & host… or beauty and the beast … or victim #1 and victim #2.
The donor motor-ectomies & electronics-ectomy will take place sometime this week. I’ve already stripped off some knick-knacks and gew gaws that I may be able to sell on eBay.
I’ve been trying to come up with a good domain name… [Jerry: right, first things first!]
I was considering metroEV.com, but the host is actually a suzuki swift (then again, my “metro” is really a “firefly”). Anyway, it’s kind of un-inspired.
We’ve toyed with suzukev, suzuki-vee, notswift, notsoswift etc., but nothing leaps out as the obvious, inspired choice.
Frankenswift? Suzukistein? Forkswift? Hey, I like that one! Ooo! Forkenswift! I just put in a call to my partner in crime and we had a good laugh over forkenswift.com.
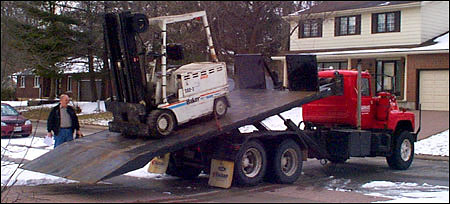
As for the forklift: it’s 16,600 lbs without the battery*. The skinny rear wheels were slowly sinking into the driveway until we borrowed a jack that could lift it, and shored it up with blocks. Happily, one can fix a brick driveway relatively easily.
(* batteries not included. with batteries, it weighed 19,700 lbs. to turn it around and park it on the edge of the driveway, I hooked together a 36V string of 12v marine batteries)
Our disclaimer is that we’re refusing to call this a conversion project until after the forklift’s motor-ectomy – when we know for sure it will fit in the swift’s engine compartment. At this point measurements look tight, but not impossible.
We’ll know more when we see how long the motor shaft is, and what’s involved in removing the safety brake assembly from the tail shaft (at least, I assume it’s connected to a tail shaft).
Until then, we’re just calling ourselves part-time junk dealers!

One thing that I have never understod was how a 20,000# electric forklift could work 8 hours/day on a single charge (including lifting 3,000# + loads repeatedly), yet a 4,000# auto cannot drive on electric power for even two hours.
I think that it is time to run the numbers on Uve’s calculator, and see what it comes up with.
Ok,
I did some checking, and you can drive either about an hour at top speed. The BIG difference is that top speed for a forklift is 22 MPH, where a vehicle would be just over 60 MPH.
At 60 MPH, the vehicle has 7.4 times the areodynamic drag of the forklift at 22 MPH. The forklift has 5.2 times the mass, and a less efficient tire/driveline combination.
So, I guess it makes sense, at least mathamatically.
Hi John,
Do they go all day without a charge? I’d always thought they either used opportunity charges or swapped out the battery pack.
Also, related to your computations, I wonder what the difference in rotational mass is between the two?
A couple threads on the matter:
* Racing tranny
* Dead weight vs. rotating weight, bike forums
* Vehicle motive models
Jerry,
When I get my Volvo 245 E-conversion underway, I will not be using any transmission at all. Not for the rotating inertia, but because of the mass and range is unaffected by gearing. I discovered this with my ‘73 Elec-Trak E12. No matter what gear you are in, the Power (Watts) used is exactly the same for the same speed.
Yes, every place that I have worked with en electric lift has gone a full shift between battery service (exchange/recharge). Now, in the “old days” you could not do this because the chargers could only get to about 80% SOC in a shift, so by 4-5 hours you needed to “top off” the pack to finnish the shift.
Glad you got that forklift info sorted out. You had me thinking I should have scrapped the Suzuki and put plates on the Baker! Now THAT would have made a head-turning grocery getter!
Update: at the end of last week, we finished removing all the electric parts from the forklift (4 motors, lots of contactors, GE EV-1 controller, potbox, 3/0 and 4/0 motor & battery cables, switches, etc.) and the scrap yard guy has already come by to pick up the bones.
Next on the list is repairing the rusty bits underneath the little Suzuki.
Looks like a good project. What size and HP are the motors? I am looking for an 8HP for my Yugo and there is a forklift shop in Dixon Il. that I want to go visit. Good luck with your car (yet)....
I have a friend Bob who has just acquired an older VW and someone just gave him a 36 volt forklift. Yep you guessed it he wants me to help him do the very thing your doing here. I am not sure the condition of the battery pack but the EverStart batteries are not that expensive. (about $50) Those are the ones I’m using in NoGas. My friend Bill use to work at a freight company (he’s retired now) and he tells me these electric fork lifts worked all day without charging. Maybe a lesser load like propelling a car will make it last all day as well. Lets hope so. DL
Hi Greg – wish i could tell you exactly what all these motors are rated at, but only the small power steering motor had specs on its motor plate (.88hp @ 48v).
The two hydraulic pump motors are 8×15 inches and 110 lbs, and the drive motor is 12×15 inches and 240 lbs. The technician who sold us the forklift said the drive motor is 10 or 12 hp continuous, and we’ll have to take his word for it unless we can figure out how find more exact info about these beasts.
By the way, your Yugo project as documented here by Jerry was a motivating factor in deciding to start this low-budget project! Please keep us updated on your motor replacement. – Darin
Hi Dr L… a FREE forklift? Man, where are people finding these deals!? Ours cost $340 (after the “recycling refund” from the scrap yard). ;-)
The individual forklift cells (we didn’t get) are very large and unusual dimensions for car use – I’m guessing 5×5x24, and must stand upright. I counted 18 in one 36V pack. Pack weight for our Baker was around 3000 lbs, and rated 1080 amp hours.
One option we’re considering is used truck batteries. A local commecial truck service center has a steady supply. The trucks they service run four 12V starting batteries each, and if one fails, they replaice all 4. Of course we’ll have to do the math to figure out if this is really a money-saving route since I have read that deeply discharging a starting battery will likely murder it in about 50 cycles… So we’d be replacing the pack every 2 or 3 months! (Or less, since the batteries aren’t new to begin with.) – D
Host car update: after poking & prodding underneath, and pulling up the carpet in the front of the little red Suzuki, we’ve decided we’re going to look for another host vehicle. Despite its nice & shiny exterior, it’s not the same picture below. There’s just way too much daylight shining in where it shouldn’t.
(You know on television when a car goes in the water and remains afloat for a few mintutes before going under? Not this car – it’d be on the bottom by the time you rolled your window down!)
We knew we were getting a rusty vehicle when we spent the $75. We were just unrealistically optimistic about the extent of it.
However, waste not, want not: since we’ll be looking for another light weight Suzuki/Metro clone, we’ll hang on to this one and scavenge what useful parts we can. And maybe sell its motor, which runs surprisingly well actually. In the mean time, we could also pull the transaxle and look at fabricating the adapter plate and a shaft coupling ahead of time…
That’s a bummer.
Then again, if you kept the car you would always have the “flintstone’s power” option if the battery should run low or you need exercise!
Host car update 2: quick turnaround on the bummer situation!
This weekend we located and purchased a better host car: a ‘92 Metro (identical body style to the red Swift), with a solid underbody, found literally two blocks from my buddy’s house. The princely sum of $175 was exchanged in the transaction.
Colour? Electric blue.
The red Swift has already made itself useful to the “new” vehicle, as the donor of a control arm / ball joint.
For the near future, we’ll be working on getting the car inspection-ready, figuring that hurdle will be easier accomplished as an ICE vehicle.
Hi all – project update!
I’m relieved to report that the donor car (#2) passed its safety standards inspection today.
This was probably the second big milestone after buying the forklift and stripping its parts. My co-conspirator and I decided the path of least resistance was to have the car inspected as an ICE vehicle, and then tackle the actual conversion after.
But even the blue car wasn’t as pristine as it looked on initial inspection. We got a little more iron, and less oxide, but there was still a fair amount of repair work to be done.
But that’s OK; I’d always wanted to learn torch brazing. And last week I practiced my newfound skill for more than a few hours repairing the Metro’s underbits).
Fortunately, my work met with the mechanic’s approval. That, plus the combination of a number of “good” parts swapped over from the red car, earned the coveted “safety check” certificate.
And in keeping with the “low-budget” goal, I’m quite happy to report we’ve already sold some of the “extra” ICE-related and other misc. parts from both cars to recover most of our vehicle costs! Certainly couldn’t do any of this without the Internet.
Next step… motorectomy part 2: ICE removal.
I think we’ve moved from “not yet” to “probably” :-D
Hello everyone,
I am planning on doing my first EV conversion. I hope to have it complete within 2 years. This is when my son will be old enough to drive at which time I will be giving him my ICE car. I will then hopefully drive the new conversion since I only travel approximately 8 miles a day. I will base my conversion on whatever parts I can find and hopefully will receive some donor parts. If anyone knowS of any donor parts please contact me at krahn@sarinc.com or call Steve at 1(262) 473-3706.I am presently starting from scratch with no parts and only a dream. Any help would be appreciated.
Thank you very much,
Steven Krahn
1234 Peninsula Ln.
Whitewater, WI 53190
262-473-3706
Update –
“Not yet”, but getting close…
In the months since my last update we’ve continued to chip away at “Project ForkenSwift”, and the car now sits in my friend’s garage, its ICE long-since removed, and the 8-inch electric pump motor mounted in its place.
We made our own adapter plate (that’s not too hard to do), and had a machinist friend modify a used LoveJoy as our coupler (integrating it with the splined clutch hub on one end – similar to Dr Larry’s approach – and the hydraulic pump shaft on the other end).
The biggest snag to date: our 2-terminal series pump motor spins the “wrong” way for the Geo transmission. We knew this before installing it, but thought (incorrectly) that we just had to reverse the polarity on the 2 terminals to run it in the other direction. No, apparently 2-terminal series motors run only in one direction, regardless of polarity. Doh!
So we need to remove the motor again and re-wire the field circuit “backwards” so it’ll go the right way. (This is one reason why 4-terminal series motors are easier to work with – you can change polarity of the field or armature by reversing the external connections.) We’ve already looked at the other pump motor, and this isn’t as big a job as it sounds. It’s a learning process.
All this is to say we may have an electric test-spin of the wheels (on jack stands) in the coming week (or so).
At which point, I will stop saying “not yet.”
Man, I just like the sound of of that product: you’re not really driving until you are driving with a Lovejoy.
When you have the motor case cranked open see if there’s a means to retard or advance the brush timing.
Our ADC motor has holes drilled in the end cap so you can unbolt it and then turn the whole end/brush assembly to offset the brushes. From the factory they come slightly advanced, presumably to provide better efficiency at higher speeds. If you are setting up for regen then typically you need to reset them back to zero.
Here’s a couple threads on the issue:
* brush timing
* ev archive
Thanks Jerry. I know we have to look at brush timing because the motor was originally wired to run one way only – so there’s a decent chance they’re not neutral (so the motor may not be properly set up to run in the other direction).
I read that one way to test for timing is to simply run the motor in both directions. If there’s no speed difference timing is neutral. If it’s faster in one direction, the brushes are advanced.
Will read those threads to gain some more edumacation. This’ll likely be this weekend’s project.
Hi Darin.
After reading your fuel saving site recently, I had a cool idea for how to implement an undertray on my Rover Metro EV (it’s here in the conversions section).
My main problem down there is a the rear two battery boxes which hang down and break up the airflow under the vehicle. Now I have been thinking for, well, probably a year about how to make an under tray to bring the entire level of the underneath to the b-box level. Nothing seemed right, fibreglass, steel or aluminium panel, even fibregrass skinned foam seemed too difficult on that scale. The closest idea, which I may still use under the rear bumper, was to spray under the floor with sticky expanding foam and then carve it to the right shape. It’s quite good. It won’t rattle or fall off like homemade fibreglass or metal panels might. It’s rigid and easy to shape. But..
I’ll tell you how I get on. I’m quite excited by the idea. As long as I can find this same building material. There’ll probably be enough foam left for me to stuff it in all the grill spaces in the front bumper as well.You can’t safety inspect the underneath of the car and you can’t service the wires / handbrake.
In 1988 when my I was 13 an my parent had a kitchen extension, there was this solid polyurethane aluminised (for vapour trap) foam bat which the builders were sawing up and putting in the wall cavity. It has a harder surface than the middle and is somewhere around 5 cm thick (from memory) It comes in maybe 4×8 feet slabs (mixing my units, sorry).
I reckon I can attach this stuff to my floor by drilling pairs of holes in it and through the floor and using goodly thick tie-wraps to loop it on through corresponding holes in the floor. this’ll squeeze the foam against the floor, each tie-wrap fixing will be a low-profile aspect to the airflow, the tie-wrap will probably recess into the foam my more than it’s thickness you can carve the sides to meet the sills in a chamfer, you can carve the top to relieve for various bits of car sticking down (e.g. handbrake cable). You can guarantee it is flat, you can make a floor for the engine compartment. Best of all, you can remove sections simply by cutting the tie-wraps and inspect there or replaces sections you have gouged on speed humps.
You can see the type of aluminised foam bat I am talking about in Peter’s Solar van (1st van picture)
I reckon I might have got the tie-wrap idea sublimininally from Peter too (see the way he attaches the plywood with nylon packing tape, 2nd van picture). I guess there’s nothing new under the sun, huh!
Interesting, James!
I’ve been thinking of using exactly the same material on my ICE car as a form for shaping a partial Kammback (which I’d then skin over with fiberglass).
Do you drive your EV fast enough to justify aero mods?
I’m not actually considering any aero improvements to the Forkenswift, mainly because I figure its average speed will only be in the 30-35 km/h range – well below speeds where aero drag forces exceed rolling & mechanical drag.
Good luck – keep us posted.
Hi Darin
Just about to go out to see if my builder’s merchant has the stuff. Yes I do drive the EV fast enough for aeromods. I go to see my parents on 60MPH trunk roads and 70MPH dual carriage ways. I tend to drive around 50 MPH, when I can because everybody else exceeds the speed limit and I think holding them up isn’t good for the EV image. THe maximum speed of my EV is about 65 MPH. When I go down hills on these fast roads I don’t want all that kinetic energy to be stolen by drag before I can convert it back to height on the way up the next hill. Know what I mean?
Jerry said: “When you have the motor case cranked open see if there’s a means to retard or advance the brush timing.”
The motor’s cranked open, and the round plate the brush pairs are attached to is fixed in one position, with no means to adv/ret the timing.
Do you think that means it’s likely that the brushes are neutral?
Well, we tested the motor today in both directions. With the field connections reversed (compared to “stock”), the motor turns much more slowly: 1480 RPM @ 12 volts, vs. 2275 RPM.
I’ve just posted a question to the EV list. Hopefully I can learn whether (a) this is a problem, and (b) if it’s fixable. (800 RPM seems to me like a huge difference to be fixed with a timing adjustment. Then again, I’ve already demonstrated I’m no expert!).
Will post back when I’ve learned more.
Dang!
Sorry for not answering you sooner. On the ADC motors the brushes are mounted to a solid rig, but the motor itself has a housing case split between main body and the end cap holding the brushes, which can be screwed back together using different offset holes. If you look at the motor pic on this page it’s the far left “silver” section which can be rotated.
Dunno if that helps or is applicable, probably not as much call for changing forklift offsets.
Our motor has the same set up – kind of. We can turn the end cap and rotate the brushes relative to the rest of the motor. But there’s only one set of screw holes on the end cap (and brush plate) – we’d have to make more to attach it in a different position.
We did try advancing/retarding the brushes while the motor was running @ 12v, and were able to make the speed change about 100 RPM or so. But not the 800 RPM difference we’re seeing between the “stock” and reversed field speeds.
I’m glad resident motor guy Jim Husted on the EV list has asked to see pics of the motor. This’ll be sorted out one way or another eventually.
The Guru has spoken.
And Mr Husted, after requesting a specific photo of the motor, suggested that the speed issue can be fixed by rotating the brush plate per his instructions.
Learned some interesting things from this: like, you can “eyeball” a motor’s brush timing by looking at where the brushes contact the commutator relative to the pole shoe bolts. E.G. if the brushes are inline with the bolts, you’ve got neutral timing (we don’t – it’s advanced for the OEM rotation).
So tomorrow I’ll likely go play with the motor and see if I can recover my “lost” 800 RPM. :)
To John G.
I was reading where you were not going to use a transmision on you EV. I am thing about trying to build me a EV and was wondering about you not using a trans. How did it turn out. Sure would thank you for a reply to solarman@alltel.net
Jerry Hood
Young Harris, GA
Does anyone have some close up pictures of timing adjustments for ADC motors they could email me or paste a link for?
Seems I’m going to have to retard the timing on the ADC FB-4001A going into the Tredia known now as “Treddles”.
:)
FYI, for anyone who may be interested: going against my general pack-rat nature, we’ve decided to sell the 12 inch drive motor we removed from the forklift. (Actually, it’s closer to 11.75 inches, but 12 sounds much more impressive.)
If you’ve been following the ForkenSwift saga, you’ll remember that we had originally planned to use this motor in the car, before discovering its diameter was slightly too big – it would have interfered with the right drive axle.
In retrospect (hey, we’re learning!), due to its heft & dimensions, this motor is probably best suited to a RWD conversion (or a FWD car with a BIG transaxle).
I’ve asked EV Motor Guru Jim Husted for a “remote evaluation” via e-mail & digital photos. So I’ve disassembled it, posted a bunch of pictures, and am waiting to hear back.
The motor’s details & images can be viewed here: 12 inch forklift motor
From the ForkenSwift link above, regarding the motor servercing near the end of it’s natural life: “Kind of like doing a hip replacement on a 98 year-old, if you know what I mean.”
LOL
Classic!
Hi, I wonder if you could help me, I can get a forklift motor without a face plate (apparently it bolts directly onto the transaxle) do you know of anyone who has made a face plate for such a motor.
Thanks
Malcolm
Just an update to close the motor topic: the 12 inch drive motor has been sold & picked up. The new owner plans to use it in an Oldsmobile Aurora. He asked for our second hydraulic pump motor also, but we’re going to hang onto it for spares.
Malcolm, just read your question. If you ever come back to read this, I have read on the EVDL of motors without face plates. Ends can be made, but the resident motor expert on the list seemed to think for the amount of work/cost involved, you’d be better off looking for some other used motor with two normal end caps.