Electric Car Safety · 27 April 08
Back when I was in the Air Force I bought a ’69 Mustang: an eight cylinder, four barreled monster…which needed “just a little work.” The AF base had a well stocked auto shop and a friend helped rebuild the engine and carb. It was a lot of fun (except for the carb!) and yet we managed to get it back together and running.
One day I was leaving our electronics shop at the end of the day. It was located out in the boonies on the other side of the runway, away from everyone else. Deciding to show off I slammed the accelerator as I left the gravel parking lot, throwing up a rooster tail of dust and squealing tires onto the asphalt road. “Ha ha” I’m sure I yelled, “eat my dust!” laughing all of the while.
I wasn’t laughing when the accelerator stayed floored after I pulled my foot away. This was a light car with a huge engine going full bore. My first instinct was to hit the brakes, which caused it to fishtail wildly towards the ditch. I didn’t want to pop it out of gear for fear that it would blow the engine. And yet it was still in a low gear and the motor wasn’t sounding very happy, the speedometer was shooting upwards, and I was having a hard time negotiating the winding rural road while formulating a plan of action.
So I shut off the ignition.
It wasn’t the first, second, or even the third thing that came to mind, and it seemed so obvious after the fact. But in the heat of the moment it can be hard to remember the obvious.
A lot of things can go wrong with a gas powered automobile: there’s a large tank of flammable gas, reservoirs of toxic fluids, extremely hot surfaces, along with spinning belts and fan blades. An EV doesn’t have the same issues — there are fewer moving parts and it doesn’t generate extreme temperatures — but there is a sizable collection of batteries and the chemistries are not much friendlier or safer than gasoline. And of course there’s all of that high voltage and current.
It’s a pretty simple equation, to move a vehicle and its contents requires a lot of energy, energy that has to be safely stored: gasoline in a tank or electrolyte in the batteries. The challenge as a designer is to contain this potential energy safely until it is needed and then transfer as much energy into moving the vehicle as possible. You’d have the exact same challenge even if the car was powered by wound up rubber bands.
As you consider converting your own electric car safety should be a primary concern, both in the construction and in the design. You will be working with quantities of voltages and chemicals that you’ve probably never had to deal with. Even for a seasoned auto mechanic the challenges are quite different.
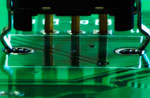
My own experience with electricity started when I was a little kid, taking everything apart and trying to understand how it worked. I worked with a radio station engineer as a teenager, followed by electronics schools and jobs with the Air Force and FAA. Over the years I’ve made mistakes, some nearly fatal, usually by being oblivious to the danger or thinking myself impervious.
When I converted the first EV, powered by twelve 12 volt batteries for 144vdc, I did my very best to be safe while working on it and also to make it safe for day to day operation. One way to approach this is to remember that you are not the only person who will be driving and working on the car. It will need to go in for inspection and, depending on your mechanic skills, may need to go into a shop for work on other parts of the car. You might want to show it to local schools or organizations. And, heaven forbid, you could get into an accident and require the aid of rescue crews.
Let’s go over the main safety issues to consider with your EV. First off some definitions:
- Pack Voltage the high voltage power used to drive the EV, usually obtained by hooking a number of 6 or 12 volt DC batteries in series.
- ACC Voltage this is the power used to power the “normal” 12vdc systems in the car, including all of the accessories.
- DC-to-DC Converter a gas powered car uses an alternator to recharge the ACC battery. Most EVs use a converter which takes the pack voltage and steps it down to 12vdc. It does this while maintaining a safe isolation between the two systems
- Fuse a metal wire or strip that melts when too much current flows through it, breaking the circuit path it is connected to (in series). One time use only.
- Circuit Breaker like a fuse, but mechanical and able to be reset after being triggered.
High Voltage
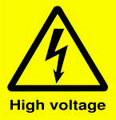
An EV will typically use 96 volts or higher to power the electric motor. Most EVs these days use 120 or 144 vdc. A few may use even higher voltages, especially those running an AC controller and motor package. In an ideal world you would be able to put all of the high voltage components, including batteries, inside a single isolating enclosure. But batteries are large and unwieldy and need to be distributed around the vehicle to balance weight, the location dictated by the few free open areas in the donor vehicle. This means high power cables running from the front to the back.
Once power leaves the batteries there’s a number of stops on the way to the motor: one or more heavy duty relays, for control and safety, shunts and fuses, and a stop at the DC controller. Even on a conservative design there’s a lot of connections and places for something to go wrong.
One of the more important aspects of making an EV is to isolate the high voltage DC from everything else, and that includes the ACC voltage used for lights and accessories. Sometimes folks try to save money by “tapping” across one of the batteries in the pack. This is very dangerous: not only do you imbalance that battery (it gets discharged faster than all of the others) but you have now connected your high voltage system to the chassis and electronics throughout the car. Let’s say you hooked across the first or last battery in a 144vdc pack. One side is hooked to negative (the car’s ground) and the other positive. It’s only twelve volts, you might think, what’s the problem? Well, yes, and no. If you take a volt meter and measure from the car’s chassis or even it’s 12vdc line to any of the other batteries you will measure high voltage. The battery furthest from the “tap” will read up to 144 volts to ground. You’ve just created a high voltage return path from any point on your car to the battery pack. Not a good isolation.
For this reason we use a DC to DC converter or even an old alternator piggy-backed to the drive motor to charge the ACC battery. It safely isolates the chassis and ACC system completely from the pack voltage. As a check you should be able to measure anywhere between the pack and the ACC system or chassis and not read a voltage.
To help maintain this isolation, even under adverse conditions (rain, rocks, collision), we use heavy duty welding cable. To combat being rubbed or nicked I also ran the cables through a thick, vinyl tube the length of the car from the back batteries to the front electronics and secured it in the “hump” where the exhaust pipe had once run. This kept it up and away from the road, and also kept it out of the passenger compartment. You, I, and most mechanics don’t expect to reach under the dash or below a strip of carpet and be exposed to high voltages. Whenever possible one should try to keep all high voltage out of the passenger compartment. Any high voltage going into the compartment should be labelled, fused, and well insulated.
If there were no such thing as accidents we’d be perfectly justified to hook up the batteries and components and leave it at that. But there are too many things that can go wrong, things outside our control, so it is best to make a little extra effort and cost to add safety measures wherever possible.
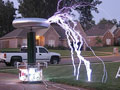
Shock potential
This is the most obvious, avoid leaving connections bare and exposed where people or tools might contact them. All of your high voltage should be shielded and labelled as such. Some of the best EV conversions put their relays, fuses, and connections inside a non-conducting panel, much like the circuit breaker box in a house. When working with batteries it is suggested that you use a short wrench, something that can’t accidentally bridge from one terminal to the next, some folks also insulate the handle to be doubly safe. In my first EV battery box there were two columns of batteries, with a high voltage from one side to the other. I put a tall insulating layer between them so a dropped tool couldn’t short the batteries.
In the Air Force all of the electronics guys were allowed to walk around with one hand in their pocket. The idea was to get in the habit of keeping one hand away from the electronics so there wasn’t a path of voltage flow from one hand to the other, across the chest. We also wore insulating boots. The equipment had safety disconnections and we clamped on grounding rods to double check that the circuit was disconnected and drained. The goal was to make sure everything was disconnected and yet still treat it as if it was live, with one hand in a pocket. All good habits to use when working on your EV.
As mentioned above it is best to try to isolate and compartmentalize the high voltage sub-system of your EV. Make it clear where the high voltage sections are and keep them as far from the rest of the car’s electrical system as possible.
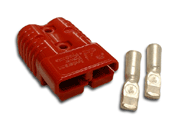
Safety Disconnects
Component failures, electronic or mechanical, are always a possibility. The circuits should be designed to disconnect the high voltage line whenever it isn’t in use and whenever there’s a problem. You’ll see most of these on the schematic page.
There should be a way to disconnect the batteries from the rest of the system. I used an Anderson connector on my first EV, better yet many folks use a circuit breaker with a mechanical cable running into the passenger compartment, doubling as a quick emergency disconnect. A fuse in the back battery compartment and one in the front handle shorts or other excess current flow failures.
A heavy duty relay hooked to the “ignition” key is used to disconnect the high voltage when the key is off. Another relay attached to the accelerator pot in the engine compartment disconnects the high voltage whenever you let off on the “gas.” In this way either letting off on the gas or turning off the key disconnects the high voltage system in the case of emergency. I also hooked an inertia switch to this circuit that turned off the relay in the case of collision.
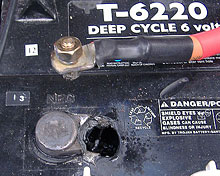
Resistance
This is an odd problem and not something you might even think of, but too much resistance can be a big problem in an EV. Since we are dealing with high voltages and high currents the one enemy is resistance. We want all of the current to go from the batteries to the motor unimpeded, any resistance along the way is going to turn into waste heat and sap our precious power. If we are designing an electric oven losing power to heat would be ok, but in an EV it is a big problem.
Depending on where you measure, an EV can pull anywhere from 200 to 500 amps, even more in a high performance or racing EV. Having any significant resistance in line with that quickly generates heat. A very common problem with a first time EV is not having all of the battery cables tightened securely or being corroded. At first it seems to work fine, but over time the connection might corrode a bit more, or expand and loosen, creating a little more resistance. Eventually the EV pulls higher current and, even through a small resistance, generates a lot of heat and melts the lead terminal, ruining the battery, maybe worse
To avoid this all connectors need to be clean. Good, solid, mechanical crimps are preferred over cheaper hammered/soldered ones. A precautionary step after tightening connectors is to drive a short bit and then check the temperature of each connector. Be careful, a bad connector could easily cause severe burns (you can use touchless thermometers). Re-check the tightness of all of the connectors. Do this over a period of a few days. As preventative maintenance be sure to look for and deal with corrosion.
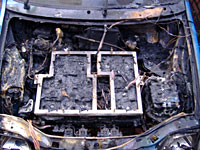
Battery Safety
I don’t have the space to offer a comprehensive guide on battery safety, they are complicated and fickle beasts and it’s best to read and heed information available from the manufacturer or via books on the subject. Each battery chemistry will have its own safety and care guidelines, even within the same chemistry you have sealed and unsealed, each having unique needs. When dealing with batteries you need to wear appropriate safety gear: glasses, gloves, apron, and so forth.
Lead acid batteries not only have caustic electrolytes, but when charging they generate hydrogen gas which is highly combustible. For this reason the battery container and the area you are charging in should be well ventilated. While hydrogen gas is lighter than air and generally dissipates quickly there shouldn’t be enclosed areas where gases can accumulate. For this reason I put a brushless DC fan on my battery box, which turned on automatically whenever the batteries were being charged cycling fresh air through the compartment. Brushless because you obviously don’t want any sparks.
Many EV converters bemoan the high cost of EV battery chargers, especially in light that they can “get away” with making a cheap, bad boy charger with a handful of electronic parts. I’ve used such a charger in a pinch, but it is anything but safe. There are no timers to shut it off, nothing to detect thermal runaway, and it isn’t customized to properly charge a specific battery chemistry. Similarly you can’t use just any charger to charge a pack of lithiums or even some of the sealed lead acid batteries. These batteries have strict charging requirements that if exceeded can easily damage or destroy them. Who wants to spend thousands (or tens of thousands in the case of Lithium) on batteries only to destroy them, and possibly your whole car?
An interesting approach being used more these day is having a bank of individual chargers, one for each battery. In this way the pile-o-batteries aren’t being treated as one big battery and there’s finer level of monitoring and control. It does increase the number of things that can go wrong (more parts and connections, increasing the chance of mistakes or failures) and you now have a big pile of chargers and wires all of which are connected to the high voltage pack.
Another safety issue with batteries is placement and containment. On one hand you don’t want the batteries in an air-tight enclosure (at least flooded lead-acid) and yet you also don’t want them bouncing around on the backseat like a load of caustic bowling balls. Lead acid batteries can weigh eighty pounds or more, not something you want flying around in an accident, nor do you want them in the passenger compartment area in an accident. Here in the northern parts of the US we have winter to contend with and keeping batteries insulated helps to retain heat and improve range.
As you can see on this page our first EV used a fiberglass reinforced plastic, double walled enclosure with insulation between the walls. The batteries themselves were held down using steel straps and rods, welded to the frame: a quarter of the batteries in the front engine compartment while the rest were enclosed in the trunk area. Another benefit of securing your batteries is that they won’t move while driving, reducing the torque and stress on the cables and connectors.

Instrumentation
One of the great things about an EV is being able to watch the meters to see exactly what is happening at any time and under any condition. Having a voltage and current meter gives you a highly useful glimpse into the “health” of your EV: is the voltage suddenly much lower than normal or the current running too high? I remember seeing a much higher current than normal on the commute to work and discovered that one of the tires was low on air.
Safety wise you’ll want to fuse the instrumentation running into the passenger compartment and make sure it is well insulated and labeled, since they will be tied into the high voltage pack. Also try to put the meters/readouts in a highly visible location, maybe replacing the normal heat and oil gauges. You’ll want to refer to these often and putting them in awkward, out of the way places isn’t safe or convenient.
Conclusion
Our Prius came with a stack of business card sized guides that outlined how to use it, to give out to auto-garages or parking attendants who might not be familiar with its key-less system. Something like that might be good for an EV as well, outlining how to operate it and where/what the safety disconnects are. While you and I may have obsessed over every little thing about EVs and motors and batteries, most folks only have a passing knowledge of what is involved and even mechanics may not have a full appreciation of the potential dangers.
For more books and references on the subject visit our EV Resources page.
By the way, the photo at the beginning of the battery section shows what was left of James May’s Rover Metro EV. He had it plugged in (outside) charging earlier this year and came out to discover it was on fire. Kind of hard to tell exactly what triggered it, but he suspects it wasn’t ventilated enough. I’ve donated some of the proceeds from this site’s ads to help him out and am looking forward to his EV Part II and more great articles from James.
Enjoy your EV and be safe!

Hi,
I think AGM batteries add to the safety. If you use the proper charger then you don’t really have to worry about hydrogen gas. You also don’t have to worry about the batteries leaking, and dissolving your car weakening or destroying it. The acid containment of the AGM batteries will also be an asset in an accident. Our car is only 48v but that’s enough to make one mighty plasma ball with only a 16 gauge wire, don’t ask me how I know :)
I have learned my lesson! It’s no more flooded batteries for me.
Great and timely article. I learnt the painful way how dangerous a big battery pack can be. Due to a small hiccup in the ignition switch wiring one side of the battery pack was earthed. When I lent over to do up the final terminal, well all I can say is it was not a pleasant feeling.
My advise to anyone connecting up any batteries is to use a multi meter and measure the voltage between anything you are going to touch and the chassis of the car or anything else likely to come in contact with your body.
I have worked with PVC conduit as used in home electrical, and I am wondering how if this could be used in an EV conversion; I am worried about wires overheating. To make the long connection between battery groups under the car, 1” (ID) conduit seems right, but if I used more conduit to make things safer, like for going into boxes, am I running the risk of wires getting too hot?